Aligning your organization
Aligning your organization around real-time, actionable intelligence is a team effort. Some key questions you need to answer are:
- Who is involved?
- What do they need?
- What problems are they trying to solve?
- What challenges do they need to overcome?
- How can you help align people in these key roles?
Begin building a list of people in your organization who need real-time insights to facilitate decisions. These are people who have responsibilities to improve quality, profitability and customer experience.
To help you build this list, we’ve identified the key roles that get involved in a typical GainSeeker deployment. Each brings their discipline-specific preconceptions to the discussions.
It is absolutely vital to keep the work at a strategic level for the benefit of the entire enterprise.
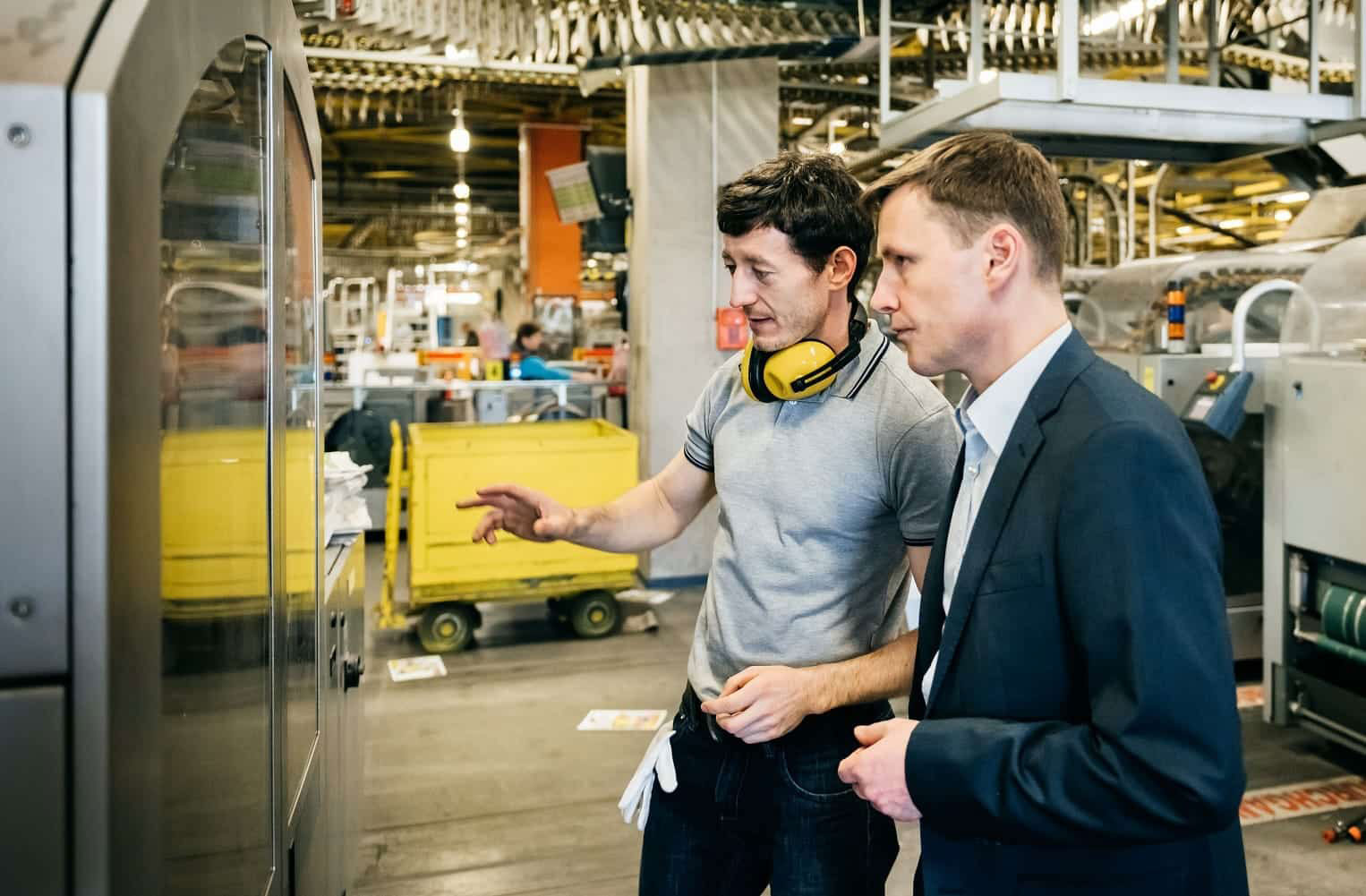
Key Roles
The roles that we’ve identified are:
- Operations leaders
- Design and manufacturing engineers
- Supply chain leaders
- Continuous Improvement and quality leaders
At this stage in your process, your goals are to:
- Lower the walls between these functions
- Foster strategic conversations
- Build a single source of truth
When this happens, you’ll see higher performance, increased supply chain flexibility, improved customer satisfaction, increased asset usage, reduced material and human costs, and increased revenue.
What are the questions and top of mind concerns about each of these roles?
Operations Leaders
In our experience, Operations Leaders (Vice Presidents/Directors of Operations, and Plant Managers) are concerned first and foremost about top and bottom line. The kinds of questions they ask are:
- How can I improve schedule adherence?
- What’s our scrap/waste/rework rates?
- How do we optimize material costs?
- How can we improve throughput and revenue?
- Can we optimize human resources?
These questions are important because increasing throughput and capacity can drive revenue (top line) growth. And better material, waste, and human cost management can drive margin (bottom line) growth.
Most leaders today recognize that they need the help of every colleague in the company to answer these questions. So, an enabling question is: “How do we build a culture of problem solving, discipline, and accountability?”
Engineering Leaders
Engineering leaders may be focused on either manufacturing engineering or on design engineering.
While there may be some overlap, manufacturing engineering wants to know if the manufacturing process is optimized for quality, productivity, and throughput. An optimized manufacturing flow increases asset utilization, reduces costs and increases quality.
Design engineering is focused more on the product and the customer. They want to know if the product design is optimized for manufacturability. They are probably also asking questions like:
- How do manufacturing defects impact customer satisfaction?
- Can design improve the customer experience?
These are important questions because a product design that is optimized for manufacturability decreases defects, increases customer satisfaction, and reduces warranty costs.
Supply Chain Leaders
Supply Chain Leaders often have the widest (or highest) perspective. They are the link between suppliers and customers. They are concerned with the entire supply chain, and the performance of each link in the chain. They are likely to be asking questions such as:
- How is quality across my supply chain?
- How can we be more responsive and flexible for our customers?
- How do we optimize pull thorough supply chain?
Continuous Improvement and Quality Leaders
Many organizations have separate functions for quality and continuous improvement. Both functions are critical to organizations.
Continuous Improvement Leaders are likely asking questions such as:
- What improvement projects should be the top priority?
- Are improvement teams productive, or do they spend all their time chasing data?
- How can we reduce project cycle times?
- Do improvements stick?
- How do we measure success?
These questions are important because they foster an organization that can identify and resolve problems better. CI teams are under pressure to deliver results, and in many organizations, projects have failed to yield the expected results. While there are many reasons for this, often isolated solutions sub-optimize the whole system.